1)以苯、碳四馏分或正丁烷为原料催化氧化制顺酐;
1) Catalytic oxidation of benzene, C4 fraction, or n-butane as raw materials to produce maleic anhydride;
2)从氧化生成的混合气中回收顺酐得到粗酐;
2) Recovering maleic anhydride from the mixture generated by oxidation to obtain crude anhydride;
3)精制粗酐从而获得顺酐产品。
3) Refine crude anhydride to obtain maleic anhydride product.
顺酐生产的技术路线主要分为苯氧化法、碳四烯烃法、苯酐副产法、正丁烷氧化法4种。下面
顺酐生产厂家为您分析:
The Technology roadmap of maleic anhydride production mainly includes benzene oxidation, C4 olefin process, phthalic anhydride by-product process and n-butane oxidation process. The manufacturer of maleic anhydride will analyze for you:
正丁烷氧化制顺酐是上近年来发展很快的正丁烷利用途径,约占顺酐总生产能力的80%。正丁烷法顺酐生产工艺按反应器分为固定床工艺和流化床工艺,其后处理工段所采用的工艺有两种技术方法,即水吸收法和溶剂吸收法。
The oxidation of n-butane to maleic anhydride is a rapidly developing way of utilizing n-butane internationally in recent years, accounting for approximately 80% of the total production capacity of maleic anhydride. The production process of n-butane maleic anhydride is divided into fixed bed process and fluidized bed process according to the reactor. There are two technical methods used in the subsequent treatment section, namely water absorption method and solvent absorption method.
1.丁烷法固定床工艺:与苯氧化法基本相似,但正丁烷氧化转化率和选择性均比苯低,其顺酐的摩尔收率按正丁烷计仅为50%~55%,而原料气体中苯和正丁烷的摩尔浓度基本相同。因此对于同样规模的生产装置,正丁烷法需要较大的反应器和压缩机。反应温度400~450℃,压力为125~130MPa。为了降低正丁烷的单耗,比利时的Pantochim公司采用尾气循环工艺,吸收塔顶出来的尾气约50%经处理后与新鲜空气一并进入反应器。该工艺可使正丁烷的单耗下降约10%。
1. Butane fixed bed process: It is basically similar to the benzene oxidation method, but the conversion and selectivity of n-butane oxidation are lower than benzene. The molar yield of maleic anhydride is only 50%~55% based on n-butane, while the molar concentrations of benzene and n-butane in the raw gas are basically the same. Therefore, for production units of the same scale, the n-butane method requires larger reactors and compressors. The reaction temperature is 400-450 ℃, and the pressure is 125-130MPa. In order to reduce the unit consumption of n-butane, Pantochim Company in Belgium adopts a tail gas circulation process. About 50% of the tail gas from the top of the absorption tower is treated and enters the reactor together with fresh air. This process can reduce the unit consumption of n-butane by about 10%.
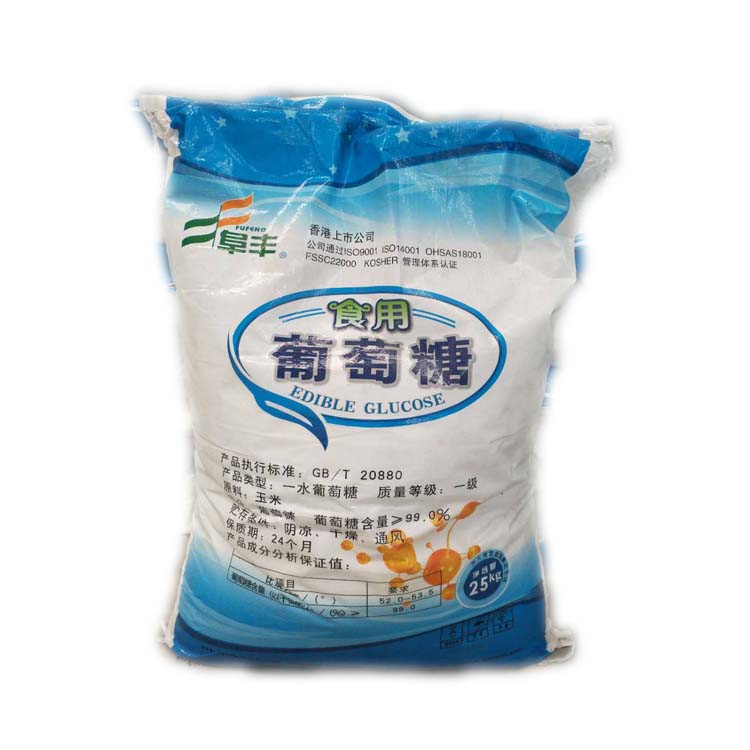
2.丁烷法流化床工艺:流化床反应器中,正丁烷和空气分别进入反应器后混合,避免了其混合时发生爆炸的可能因此原料气中正丁烷的摩尔分数可以提高到4%,反应所需空气约为固定床的一半,减少了空气压缩机的投资和操作费用。流化床工艺的能耗低于固定床,但丁烷的单耗要比固定床高约8%,另外流化床催化剂的磨损也较大。
2. Butane method fluidized bed process: in the fluidized bed reactor, n-butane and air are mixed after entering the reactor respectively, avoiding the possibility of explosion during mixing. Therefore, the Mole fraction of n-butane in the feed gas can be increased to 4%, and the air required for reaction is about half of the fixed bed, reducing the investment and operating costs of the air compressor. The energy consumption of the fluidized bed process is lower than that of the fixed bed, but the unit consumption of butane is about 8% higher than that of the fixed bed, and the wear of the fluidized bed catalyst is also significant.
3.有机溶剂吸收法工艺:在采用丁烷法生产顺酐的初期,主要是一些苯法装置通过更换催化剂实现,就是新建的装置工艺也与苯法基本一致,均为水吸收法回收。由于丁烷氧化反应生成少量的乙酸和丙烯酸,而苯氧化反应几乎不生成乙酸和丙烯酸,另外丁烷氧化生成的水也比苯氧化多1倍,所以丁烷法水吸收工艺遇到的腐蚀和堵塞问题要比苯法多。
3. Organic solvent absorption process: In the early stages of using the butane method to produce maleic anhydride, some benzene process units were mainly achieved by replacing catalysts, and even the newly built unit process was basically the same as the benzene process, all of which were recovered by water absorption method. Due to the butane oxidation reaction generating a small amount of acetic acid and acrylic acid, while the benzene oxidation reaction hardly generates acetic acid and acrylic acid, and the amount of water generated by butane oxidation is also twice that of benzene oxidation, the butane method water absorption process encounters more corrosion and blockage problems than the benzene method.
在工业生产中,这两种溶剂的消耗接近,DIBE溶剂处理需进行水洗和碱洗两个过程,而DBP溶剂仅需水洗。另外,DIBE的要高于DBP。更多相关事项就来我们网站
http://chaonvhui.com咨询看看吧!
In industrial production, the consumption of these two solvents is similar. DIBE solvent treatment requires two processes: water washing and alkali washing, while DBP solvent only requires water washing. In addition, the price of DIBE is higher than that of DBP. For more related matters, come to our website http://chaonvhui.com Consult and take a look!